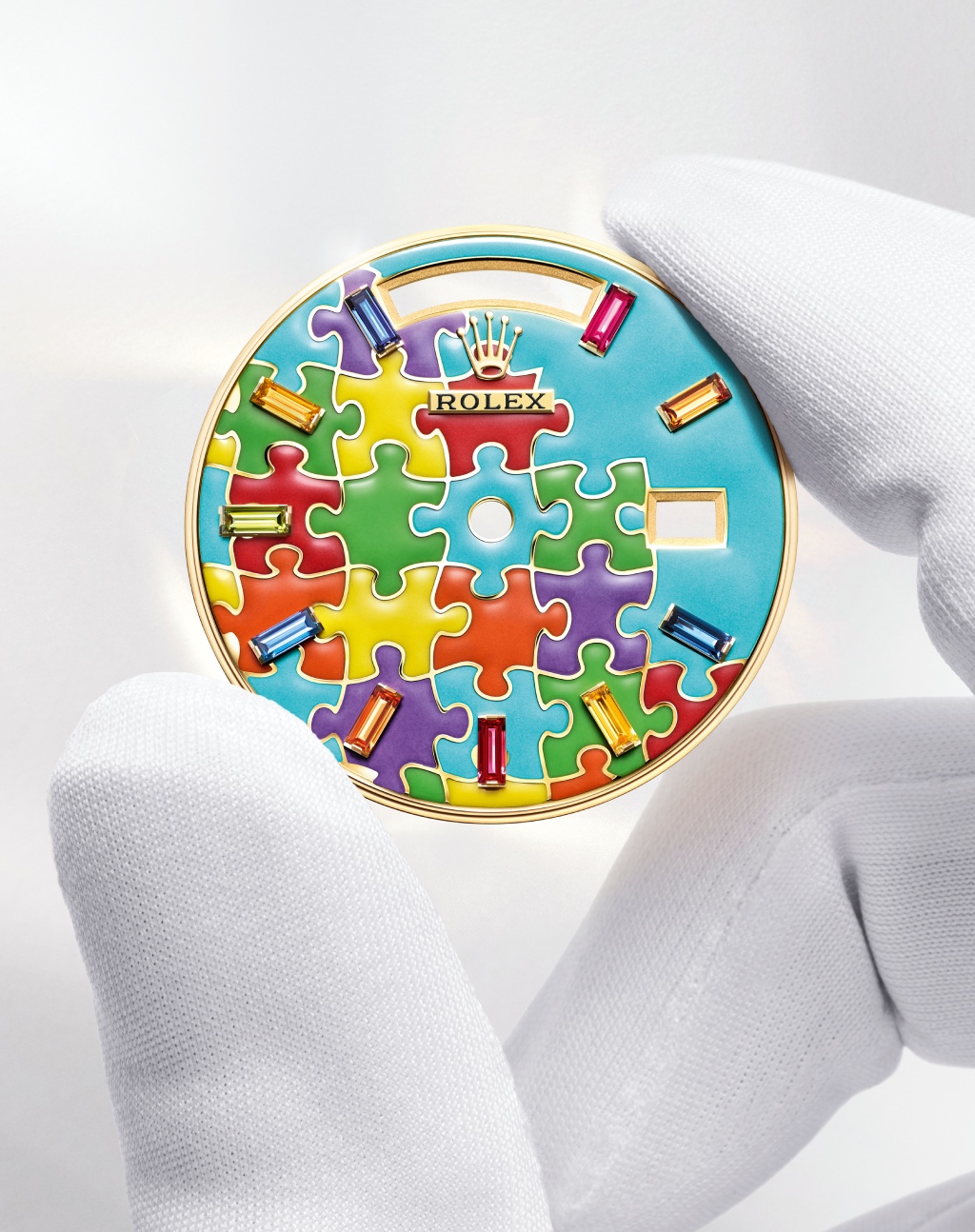
It would not be an exaggeration to say that the dial makes the watch face: it supports reading time and other measurements, but it is so much more than a practical feature—it is a canvas for creative expression. A highly visible portion of a watch, the dial establishes the aesthetic identity of the timepiece, and its design can even be emblematic of certain models and references. By expressing balance, cohesion and harmony among its various elements and attributes, the dial serves not only as a measure of a watchmaker’s attention to detail and commitment to craftsmanship, but as a miniature work of art that showcases extraordinary decorative techniques and profound design philosophies.
The creation of the dial even bears its own name, art cadranier, and Rolex is a master of this craft. Orchestrated by its massive team of some 500 devoted entirely to dial-making—experts specialising in areas such as gemsetting, painting, and engineering—Rolex’s dial production is done entirely in house at the dedicated facility in Chêne-Bourg, Geneva.
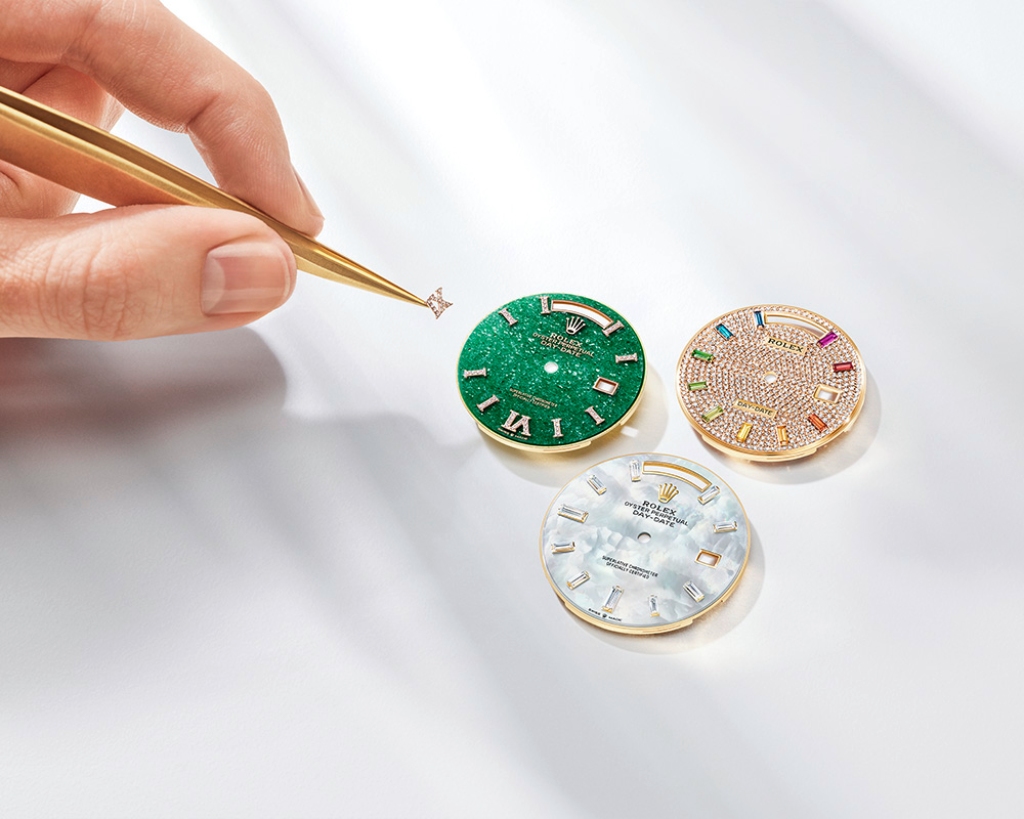
Starting with an original idea, which goes through revision, experimentation and refinement, the blueprint drawing of a dial design takes form. The dial development team, under research and development, turns that design into a prototype, through collaboration among designers, engineers and subject matter experts. Out of hundreds of dial prototypes built every year, only a few are eventually added to the brand catalogue.
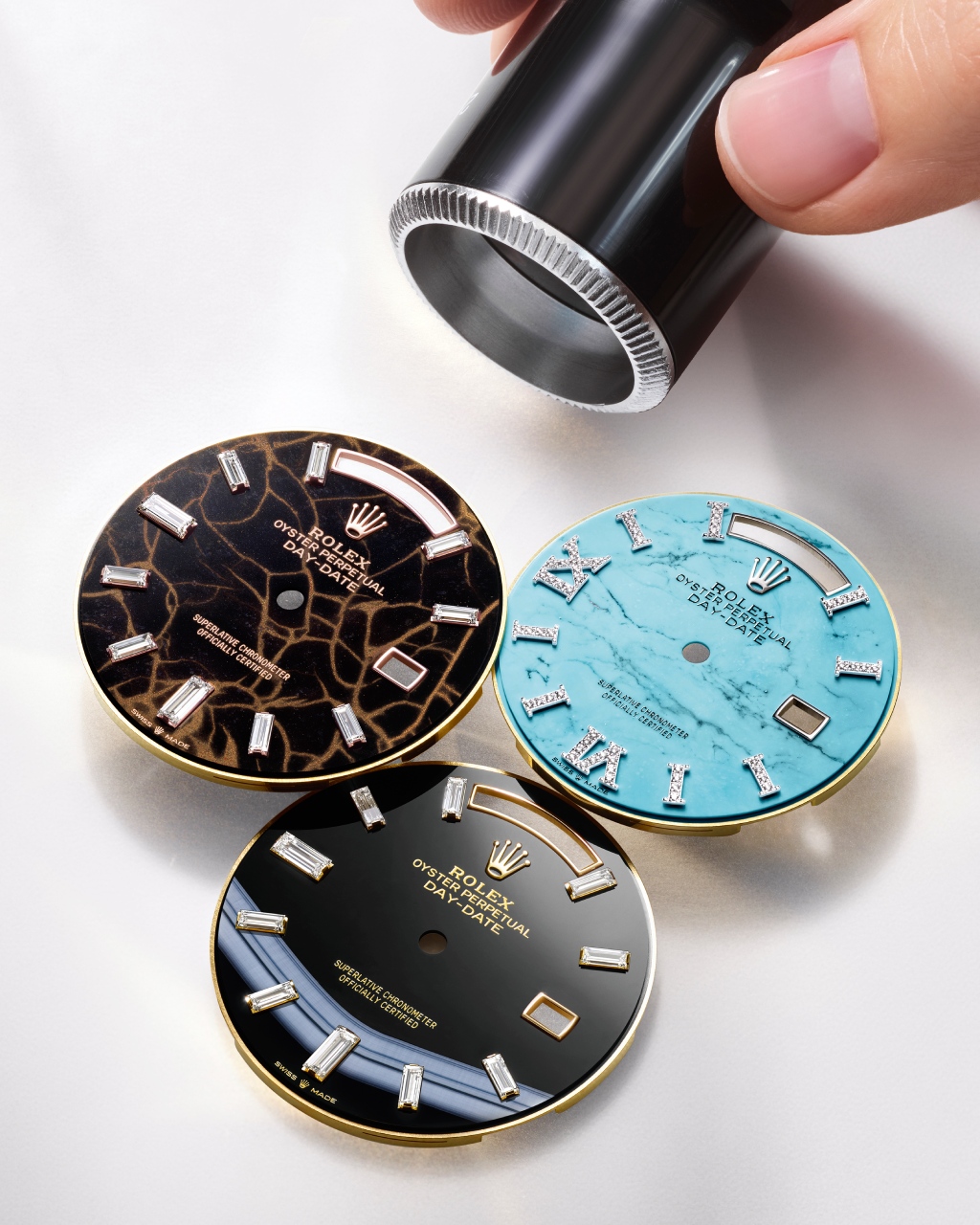
The process begins with a brass medallion, which can be finished in precious metals such as 18ct yellow gold, 18ct white gold and 18ct Everose gold, or materials like mother-of-pearl or meteorite and coloured hardstones from green aventurine to turquoise, and even paved with gemstones or set with gemstone hour markers. Pad printing, often used to print the desired text and symbols on the dial, is sometimes also used to create decorations, such as the ‘Celebration’ motif made up of colourful bubbles introduced last year in the Oyster Perpetual range.
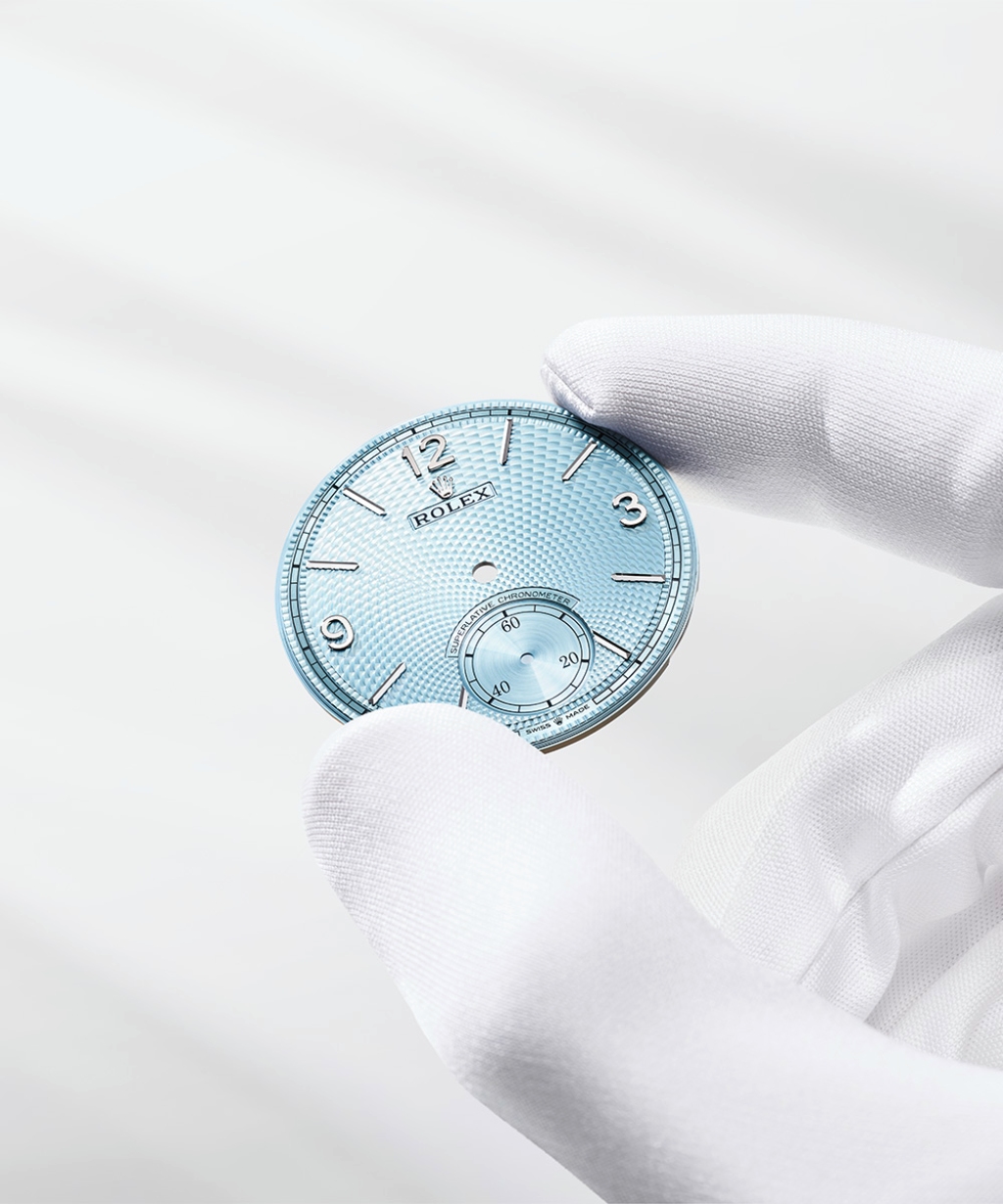
Going even further, a suite of specialised techniques are employed to create spectacular coloured dials: lacquering, with pigment airbrushed onto the brass dial in fine layers, generates a spectrum of bold opaque colours; electroplating thin layers of metals creates colours like silver, champagne, slate and steel; and PVD (Physical Vapour Deposition), which covers a brass dial with metal oxide alloys or nitrides—a layer of atoms less than a micron thick—goes further than electroplating by producing rich colours like olive and chocolate or subtle ones like ice blue and pale pink. There is also grand feu enamelling, a complex metier d’art applied to intricate dial decoration, resulting in intense colours that remain stable over time; a recent example is the vibrant puzzle motif dial on the Oyster Perpetual Day-Date 36 released last year to great acclaim.
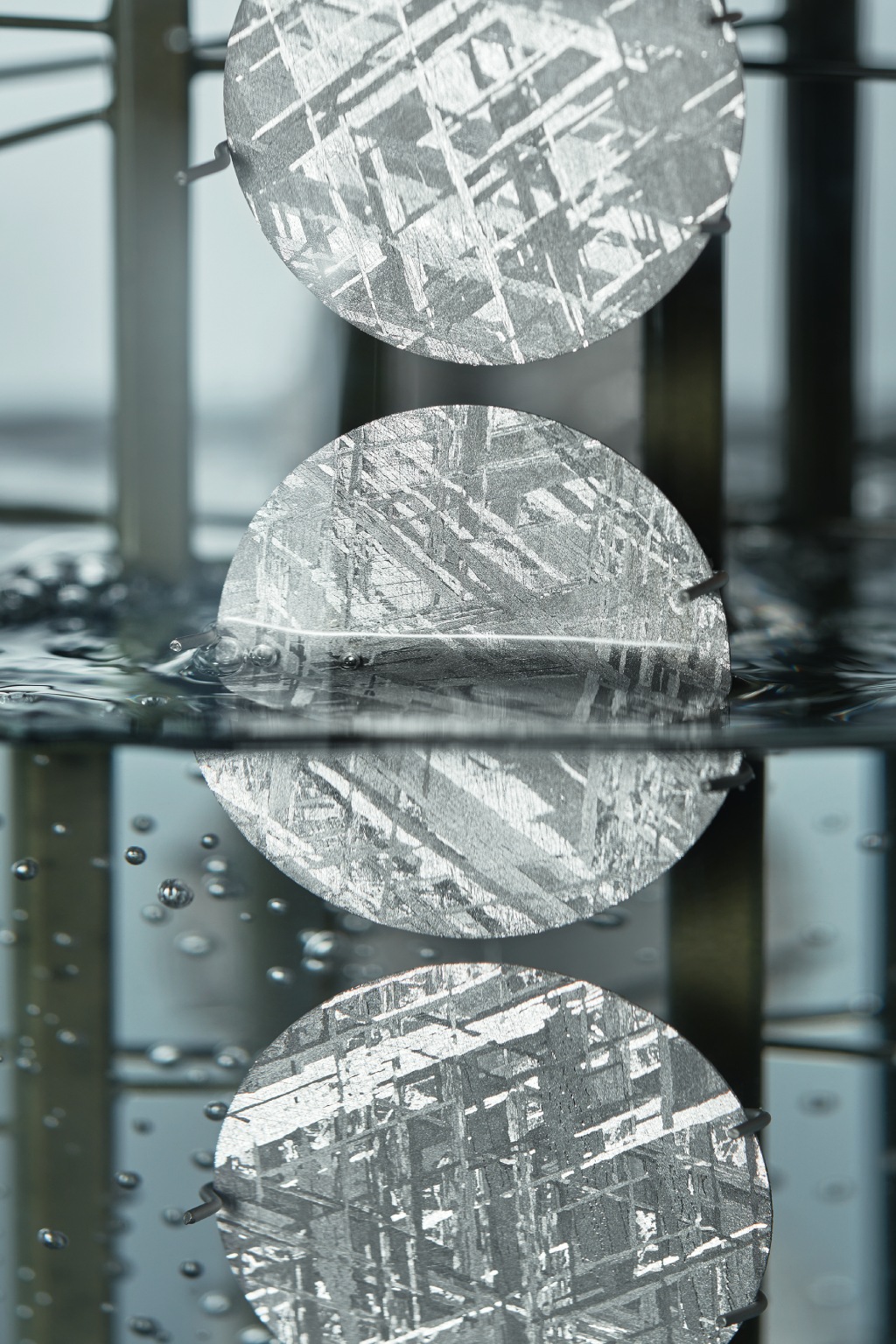
Beyond colour, the final surface finishing of the dial can influence its appearance too. A sunray finish made up of fine radial lines or a satin finish composed of minute parallel lines can create different effects when light strikes the dial. And even with dials of the same colour, a matt varnish exudes a more sporty energy, while a glossy varnish channels more sophistication.
This story originally appeared in the June/July 2024 issue of GRAZIA Singapore.
READ MORE
Backstory: How The Boucheron Quatre Continually Reimagines Its 4-Design Motif
Exclusive: What Do Han So-Hee, Kaia Gerber And Liu Shishi Really Think About Diamonds On Watches?
Deepika Padukone Is The Face Of Cartier’s Latest High Jewellery Collection, Nature Sauvage